
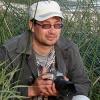
Наша жизнь в Германии. Немного о производстве гигантской керамической плитки
Написано vadim69,
28 April 2025
·
27 просмотров
И так…
Прежде чем продолжить, я должен исполнить одну формальность.
Всё, о чём я здесь пишу - только лишь мой персональный взгляд на происходившее. О том, что на самом деле происходило в стенах и за стенами нашего предприятия, я могу судить лишь по тем немногим крупицам информации, которые долетали в производственный цех. И я могу даже предположить, что на самом деле реального представления о нашем предприятии не имел ни кто.
И ещё. Повторюсь. Наше предприятие не являлось характерным для Германии случаем. Скорее - исключение из правил. Но… Даже исходя из того, что на нём происходило, можно судить о многих аспектах жизни в Германии. Как мне кажется.
Первый рабочий день начался для нашей группы новеньких с экскурсии по предприятию.
Думаю, что нам с вами тоже будет не лишним сделать такую экскурсию. Лично мне было очень интересно. Но одно дело видеть всё своими глазами, а другое дело - читать об этом. Но экскурсия нужна для лучшего понимания событий, о которых пойдёт речь.
Не знаю - на сколько глубоко я должен погружаться в технические аспекты. Поэтому извиняюсь за возможные излишества.
И так. Представьте. Предприятие длинной 800 метров. С пристройкой здания бюро в начале (или в конце?) и с несколькими пристройками в конце (или в начале?). Где конец и где начало у предприятия - с этим всегда была путаница. Поскольку вход на завод был через здание бюро. Но… Технологический процесс начинался в другом конце. А в районе бюро шла уже упаковка готовой плитки. Может эта путаница в элементарных вещах таки и привела нас к закрытию?! Кто знает…
По предприятию было принято перемещаться на велосипедах. Даже первая статья о нас в местной газете так и называлась - "На велосипеде по заводу"
Но мы, новенькие, в тот день шли пешком.
Нас привели в другой конец предприятия. Вывели на улицу. Там, под большим навесом, огороженным с трёх сторон, располагалось хранилище сырья и производственных отходов. Помещение делилось на боксы толстыми бетонными простенками.
Три бокса были отведены под материал для керамики. Вот тут я - двоечник. Поскольку прослушал, о чём говорили. Материал меня мало интересовал. На внешний вид он был весь одинаковый. Песок себе и песок. Говорят, что один сорт песка привозился спецом из Австралии. Или из Новой Зеландии?! Не важно…
Остальные два бокса были отведены под отходы. Один под трокенбрух - для керамической массы не прошедшей печку. А последний - для битой плитки.
Специальным погрузчиком, который позволял взвешивать материал прямо в ковше, ингредиенты в определённой пропорции загружались в металлический контейнер со шнекой (спиралью для подачи). Из контейнера материал попадал на транспортёрную ленту и далее следовал в ауфберайтунг - цех по производству керамического гранулата.
Ауфберайтунг - самая крупная пристройка к основному заводскому зданию. Здесь есть много чего интересного. Но нас интересуют сейчас барабаны для получения шликера - керамической жижи.
Всего их 4 штуки. Размер примерно 5*5 метров каждый. Туда уже загружены керамические шары. В зависимости от запросов шары могут быть разного диаметра. От 20 до 60 мм. И вот сюда, через специальный портал, поступают ингредиенты из хранилища. Сюда же иногда добавлялась краска. Это если планировалось большое производство, к примеру, чёрной плитки. Затем в барабан заливалось несколько кубов воды. И начинался процесс перемалывания ингредиентов до порошка. Грохот в аубирайтунге стоит в такие моменты….
Материал должен быть перемолот до определённых параметров. Для этого периодически барабаны останавливают, берут пробы и несут в лабораторию.
Когда шликер готов, его сливают в подземные танки (резервуары). Танки эти круглой формы, что бы там мог вращаться специальный размешиватель. Шликер нужно постоянно перемешивать. Иначе он расслоится и… У нас будут проблемы… Чистить танк. Вы и представить себе не можете - какая это развлекаловка!!! Раза три я принимал участие…
И вот шликер готов. Теперь из подземелья его подают на самый верх. Почти под крышу. И через специальные брызгалки распыляют внутри огромной цилиндрической башни. Эти башня имеет снизу конус. А в центре располагается газовая горелка. И так, мелкие капли шликера летят вниз, попадают в горячий воздух, создаваемый горелкой, и влетают в конус уже в сухом виде, в виде гранул.
Уже готовый гранулат высыпается из башни на транспортёрную ленту и отправляется в эскалатор, который отправляет гранулат на самый верх, под крышу, откуда он специальной системой распределения, рассыпается по десяти зилосам - огромные вертикальные цилиндры в два ряда, для хранения гранулата. Очень напоминает картинки с элеваторами.
В этих зилосах можно хранить сотни тонн гранулата. Но даже такого запаса нам, при полной загрузке, хватило бы лишь на несколько дней.
Теперь запас гранулата сделан и мы можем приступать непосредственно к производству плитки.
Снизу каждый зило имеет конус. Из конуса гранулат подаётся на транспортёрную ленту и уходит на другой эскалатор. Опять гранулат поднимается на самый верх и следует уже в другой, основной цех. Здесь он поступает в миштурм. Смесительную башню.
Миштурм - сложное высокое сооружение в пять этажей, где происходит сразу несколько технологических процессов.
Сначала гранулат поступает в зило. Точнее их два. Завод имеет две идентичные и параллельные производственные линии. Поэтому начиная с миштурма уже начинается разделение подаваемого материала на две линии и сама конструкция миштурма - зеркальная.
Но что бы в этом не заблудиться, далее я буду говорить только об одной линии и одной половине.
И так, миштурм имеет своё собственное небольшое зило. Всего на 9 тонн. Это буфер материала, который должен постоянно пополняться. Из малого зило гранулат по специальной ленте движется через весы. На весах гранулат взвешивается и компютер получает два параметра. Вес гранулата и скорость ленты. Это позволяет ему достаточно точно дозировать количество гранулата для дальнейшего смешивания.
И так, компьютер забирает у зило определённое количество гранулата. Стандартно - 400 кг. По пути есть специальная линия, где можно добавлять в гранулат краску. Теперь эта порция поступает в мишер. Смеситель.
На одну линию - четыре смесителя. Доза сухого гранулата засыпается в смеситель. Туда же заливается вода. Строго определённое количество. Плюс/минус 2 десятые по влажности и масса становится непригодной для производства. Начинается процесс смешивания.
Полученная масса должна быть определённой консистенции. Небольшие рыхлые клубки до 5-ти см. Но при сжатии руками такая масса должна легко склеваться в плотный комок глины.
Готовая масса ссыпается из мишера в специальный приёмник-дозатор. Здесь опять расположены весы. Что бы компьютер знал - сколько материала загружено на ленту. И уже отсюда готовая масса попадает на ленту и следует в самое сердце производственного процесса - экструдер.
Экструдер, по сути - это большая сложная мясорубка. Только вместо мяса здесь - керамическая масса.
Сверху расположен трихтер - воронка. Сюда ссыпается масса. Масса сразу попадает на два длинных шнека - подающие спирали и заползает вглубь экструдера.
На концах шнеков расположены груглые лепестковые ножи. Они нарезают выползающую массу на мелкие части. И масса попадает в камеру, из которой откачивается воздух. Создаётся вакуум. Далее специальные вращающиеся эксцентрические захваты подминают массу и утягивают вниз, к основной, толстой шнеке - спирали.
От этой шнеки масса выползает гигантской колбасой, диаметром примерно 60см. И специальная насадка начинает плющить эту массу, придавая ей горизонтальную и всё более узкую и форму.
Очень важно, что бы давление в массе распределялось равномерно. поэтому в кострукцию встроены специальные бремзы - тормоза. Они прикрывают проход для массы в центре и давление распределяется ближе к краям.
Уже на выходе из насадки цепляется специальная пластина с тормозной системой более тонкой настройки. Здесь равномерность давления массы настраивается с большой точностью. Иначе… Это надо видеть. Иначе мы получим волны то в центре плитки, то с краю. Красиво, но….
На вторые бремзы надевается мундштук. Тут, вероятно, перевода не надо…
Мундштук представляет собой плату из массивного металла и горизонтальной прорезью по середине. именно эта прорезь и придаёт плитке её окончательный вид и качество поверхности.
Длинна прорези примерно 130-140 см. Это и задаёт базовый формат. В итоге что-то будет обрезано, что то - откалибровано, а на выходе мы получаем 120 см. Это только в ширину. А базовая длинна плитки на тот момент составляла 240см. Выше человеческого роста, на секундочку…
И так, полученная масса проталкивается через мундштук и оказывается на транспортном столе. Или стол с роликами. По роликам масса выползает всё дальше. Пока компьютер не намеряет нужную длину. Тогда срабатывал проволочный порезчик и уже отрезанная плитка двигалась дальше. Дальше она попадала в мой родной Ньютек - машину, по нанесению рисунка и прозрачной глазури. Далее следовала на порезочный стол, где ей задавали более точные размеры и, если необходимо, разрезали на более мелкую плитку.
Далее плитка двигалась в предварительную инфракрасную сушилку, толку от которой было, впрочем, крайне мало. И со временем её просто демонтировали.
Далее плитка попадала в трокнер - сушилку. Там она специальным лифтом распределялась на пять этажей и очень медленно начинала двигаться в трокнере. Задача трокнера - не просто просушить плитку, а придать плитке определенную влажность. Что бы плитка была готова следовать в печку.
Между трокнером и печкой был промежуток метров 20. С печкой всё сложнее, чем с трокнером. Здесь плитка может двигаться только в один ряд. А температуру надо поднимать очень постепенно. Поэтому печка - это самая длинная часть предприятия. Имеет множество секторов. У каждого сектора - своя температура. Самая высокая температура - 1500 градусов. Понижается температура так же постепенно.
После печки плитка отправляется на отдых и окончательное остывание. В специальные боксы. А боксы эти развозят специальные роботы. Вот эти двое, таки создавали современное лицо предприятия. Это производит впечатления, когда два самодвижущихся робота сами забирают полные контейнеры и привозят и устанавливают на место пустые. Если бы всё предприятие работало, как эти два робота. Эх!...
Из контейнеров плитка направлялась на калибровку.
Калибровали плитку две машины. Одна машина под длинные стороны, другая - под короткие. Плитка заходила в машину, выставлялась ровно, захватывалась сверху и снизу прижимными движущимися лентами и подавалась на калибраторы - алмазные диски, вращающиеся с большой скоростью. Шум там был!!!! Самое шумное место на предприятии. Без наушников долго не простоять.
Цель калибровки - задать плитке точный размер и точный угол.
На одной из линий стояла специальная машина по полировке плитки. Полированная плитка - это одна из разновидностей плиток со своими свойствами и особенностями. К тому же весьма проблемная в производстве.
Машина начинала с того, что…. обгрызала с плитки верхний слой. Буквально. Занимался этим специальный валик с алмазными зубьями, оставлявший на поверхности плитки борозды. За тем две шлифовальные головы убирали эти борозды. А затем начинался процесс тонкой шлифовки и окончательной полировки.
Если удавалось получить хоть какое-то количество готовой плитки, то она следовала на упаковку.
Паковал плитку робот. Но здесь были постоянные проблемы. За машиной надо было постоянно следить и подстраивать. Но это что касалось мелкой плитки. 120/60 или меньше. А вот крупную приходилось упаковывать вручную. Специальным краном с рамой и вакуумными присосками плитка снималась со стола и устанавливалась на специальные козлы.
Ну вот… Плитка произведена и упакована. Теперь бы её как-нибудь продать. А вот с этим начинались реальные проблемы…
В инфракрасной печи...
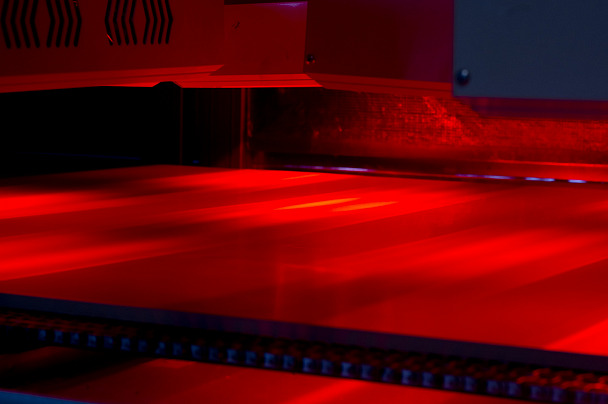
оформляем выставочный зал.
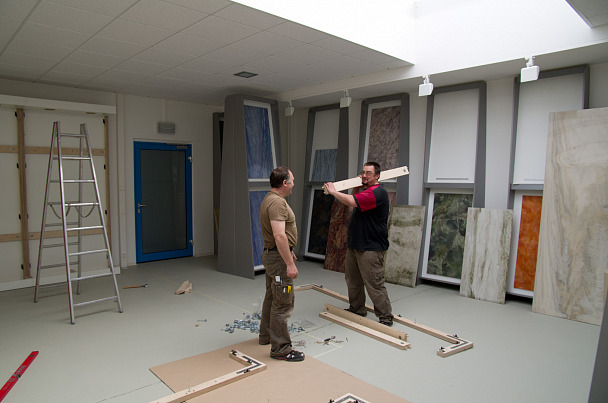
Прежде чем продолжить, я должен исполнить одну формальность.
Всё, о чём я здесь пишу - только лишь мой персональный взгляд на происходившее. О том, что на самом деле происходило в стенах и за стенами нашего предприятия, я могу судить лишь по тем немногим крупицам информации, которые долетали в производственный цех. И я могу даже предположить, что на самом деле реального представления о нашем предприятии не имел ни кто.
И ещё. Повторюсь. Наше предприятие не являлось характерным для Германии случаем. Скорее - исключение из правил. Но… Даже исходя из того, что на нём происходило, можно судить о многих аспектах жизни в Германии. Как мне кажется.
Первый рабочий день начался для нашей группы новеньких с экскурсии по предприятию.
Думаю, что нам с вами тоже будет не лишним сделать такую экскурсию. Лично мне было очень интересно. Но одно дело видеть всё своими глазами, а другое дело - читать об этом. Но экскурсия нужна для лучшего понимания событий, о которых пойдёт речь.
Не знаю - на сколько глубоко я должен погружаться в технические аспекты. Поэтому извиняюсь за возможные излишества.
И так. Представьте. Предприятие длинной 800 метров. С пристройкой здания бюро в начале (или в конце?) и с несколькими пристройками в конце (или в начале?). Где конец и где начало у предприятия - с этим всегда была путаница. Поскольку вход на завод был через здание бюро. Но… Технологический процесс начинался в другом конце. А в районе бюро шла уже упаковка готовой плитки. Может эта путаница в элементарных вещах таки и привела нас к закрытию?! Кто знает…
По предприятию было принято перемещаться на велосипедах. Даже первая статья о нас в местной газете так и называлась - "На велосипеде по заводу"
Но мы, новенькие, в тот день шли пешком.
Нас привели в другой конец предприятия. Вывели на улицу. Там, под большим навесом, огороженным с трёх сторон, располагалось хранилище сырья и производственных отходов. Помещение делилось на боксы толстыми бетонными простенками.
Три бокса были отведены под материал для керамики. Вот тут я - двоечник. Поскольку прослушал, о чём говорили. Материал меня мало интересовал. На внешний вид он был весь одинаковый. Песок себе и песок. Говорят, что один сорт песка привозился спецом из Австралии. Или из Новой Зеландии?! Не важно…
Остальные два бокса были отведены под отходы. Один под трокенбрух - для керамической массы не прошедшей печку. А последний - для битой плитки.
Специальным погрузчиком, который позволял взвешивать материал прямо в ковше, ингредиенты в определённой пропорции загружались в металлический контейнер со шнекой (спиралью для подачи). Из контейнера материал попадал на транспортёрную ленту и далее следовал в ауфберайтунг - цех по производству керамического гранулата.
Ауфберайтунг - самая крупная пристройка к основному заводскому зданию. Здесь есть много чего интересного. Но нас интересуют сейчас барабаны для получения шликера - керамической жижи.
Всего их 4 штуки. Размер примерно 5*5 метров каждый. Туда уже загружены керамические шары. В зависимости от запросов шары могут быть разного диаметра. От 20 до 60 мм. И вот сюда, через специальный портал, поступают ингредиенты из хранилища. Сюда же иногда добавлялась краска. Это если планировалось большое производство, к примеру, чёрной плитки. Затем в барабан заливалось несколько кубов воды. И начинался процесс перемалывания ингредиентов до порошка. Грохот в аубирайтунге стоит в такие моменты….
Материал должен быть перемолот до определённых параметров. Для этого периодически барабаны останавливают, берут пробы и несут в лабораторию.
Когда шликер готов, его сливают в подземные танки (резервуары). Танки эти круглой формы, что бы там мог вращаться специальный размешиватель. Шликер нужно постоянно перемешивать. Иначе он расслоится и… У нас будут проблемы… Чистить танк. Вы и представить себе не можете - какая это развлекаловка!!! Раза три я принимал участие…
И вот шликер готов. Теперь из подземелья его подают на самый верх. Почти под крышу. И через специальные брызгалки распыляют внутри огромной цилиндрической башни. Эти башня имеет снизу конус. А в центре располагается газовая горелка. И так, мелкие капли шликера летят вниз, попадают в горячий воздух, создаваемый горелкой, и влетают в конус уже в сухом виде, в виде гранул.
Уже готовый гранулат высыпается из башни на транспортёрную ленту и отправляется в эскалатор, который отправляет гранулат на самый верх, под крышу, откуда он специальной системой распределения, рассыпается по десяти зилосам - огромные вертикальные цилиндры в два ряда, для хранения гранулата. Очень напоминает картинки с элеваторами.
В этих зилосах можно хранить сотни тонн гранулата. Но даже такого запаса нам, при полной загрузке, хватило бы лишь на несколько дней.
Теперь запас гранулата сделан и мы можем приступать непосредственно к производству плитки.
Снизу каждый зило имеет конус. Из конуса гранулат подаётся на транспортёрную ленту и уходит на другой эскалатор. Опять гранулат поднимается на самый верх и следует уже в другой, основной цех. Здесь он поступает в миштурм. Смесительную башню.
Миштурм - сложное высокое сооружение в пять этажей, где происходит сразу несколько технологических процессов.
Сначала гранулат поступает в зило. Точнее их два. Завод имеет две идентичные и параллельные производственные линии. Поэтому начиная с миштурма уже начинается разделение подаваемого материала на две линии и сама конструкция миштурма - зеркальная.
Но что бы в этом не заблудиться, далее я буду говорить только об одной линии и одной половине.
И так, миштурм имеет своё собственное небольшое зило. Всего на 9 тонн. Это буфер материала, который должен постоянно пополняться. Из малого зило гранулат по специальной ленте движется через весы. На весах гранулат взвешивается и компютер получает два параметра. Вес гранулата и скорость ленты. Это позволяет ему достаточно точно дозировать количество гранулата для дальнейшего смешивания.
И так, компьютер забирает у зило определённое количество гранулата. Стандартно - 400 кг. По пути есть специальная линия, где можно добавлять в гранулат краску. Теперь эта порция поступает в мишер. Смеситель.
На одну линию - четыре смесителя. Доза сухого гранулата засыпается в смеситель. Туда же заливается вода. Строго определённое количество. Плюс/минус 2 десятые по влажности и масса становится непригодной для производства. Начинается процесс смешивания.
Полученная масса должна быть определённой консистенции. Небольшие рыхлые клубки до 5-ти см. Но при сжатии руками такая масса должна легко склеваться в плотный комок глины.
Готовая масса ссыпается из мишера в специальный приёмник-дозатор. Здесь опять расположены весы. Что бы компьютер знал - сколько материала загружено на ленту. И уже отсюда готовая масса попадает на ленту и следует в самое сердце производственного процесса - экструдер.
Экструдер, по сути - это большая сложная мясорубка. Только вместо мяса здесь - керамическая масса.
Сверху расположен трихтер - воронка. Сюда ссыпается масса. Масса сразу попадает на два длинных шнека - подающие спирали и заползает вглубь экструдера.
На концах шнеков расположены груглые лепестковые ножи. Они нарезают выползающую массу на мелкие части. И масса попадает в камеру, из которой откачивается воздух. Создаётся вакуум. Далее специальные вращающиеся эксцентрические захваты подминают массу и утягивают вниз, к основной, толстой шнеке - спирали.
От этой шнеки масса выползает гигантской колбасой, диаметром примерно 60см. И специальная насадка начинает плющить эту массу, придавая ей горизонтальную и всё более узкую и форму.
Очень важно, что бы давление в массе распределялось равномерно. поэтому в кострукцию встроены специальные бремзы - тормоза. Они прикрывают проход для массы в центре и давление распределяется ближе к краям.
Уже на выходе из насадки цепляется специальная пластина с тормозной системой более тонкой настройки. Здесь равномерность давления массы настраивается с большой точностью. Иначе… Это надо видеть. Иначе мы получим волны то в центре плитки, то с краю. Красиво, но….
На вторые бремзы надевается мундштук. Тут, вероятно, перевода не надо…
Мундштук представляет собой плату из массивного металла и горизонтальной прорезью по середине. именно эта прорезь и придаёт плитке её окончательный вид и качество поверхности.
Длинна прорези примерно 130-140 см. Это и задаёт базовый формат. В итоге что-то будет обрезано, что то - откалибровано, а на выходе мы получаем 120 см. Это только в ширину. А базовая длинна плитки на тот момент составляла 240см. Выше человеческого роста, на секундочку…
И так, полученная масса проталкивается через мундштук и оказывается на транспортном столе. Или стол с роликами. По роликам масса выползает всё дальше. Пока компьютер не намеряет нужную длину. Тогда срабатывал проволочный порезчик и уже отрезанная плитка двигалась дальше. Дальше она попадала в мой родной Ньютек - машину, по нанесению рисунка и прозрачной глазури. Далее следовала на порезочный стол, где ей задавали более точные размеры и, если необходимо, разрезали на более мелкую плитку.
Далее плитка двигалась в предварительную инфракрасную сушилку, толку от которой было, впрочем, крайне мало. И со временем её просто демонтировали.
Далее плитка попадала в трокнер - сушилку. Там она специальным лифтом распределялась на пять этажей и очень медленно начинала двигаться в трокнере. Задача трокнера - не просто просушить плитку, а придать плитке определенную влажность. Что бы плитка была готова следовать в печку.
Между трокнером и печкой был промежуток метров 20. С печкой всё сложнее, чем с трокнером. Здесь плитка может двигаться только в один ряд. А температуру надо поднимать очень постепенно. Поэтому печка - это самая длинная часть предприятия. Имеет множество секторов. У каждого сектора - своя температура. Самая высокая температура - 1500 градусов. Понижается температура так же постепенно.
После печки плитка отправляется на отдых и окончательное остывание. В специальные боксы. А боксы эти развозят специальные роботы. Вот эти двое, таки создавали современное лицо предприятия. Это производит впечатления, когда два самодвижущихся робота сами забирают полные контейнеры и привозят и устанавливают на место пустые. Если бы всё предприятие работало, как эти два робота. Эх!...
Из контейнеров плитка направлялась на калибровку.
Калибровали плитку две машины. Одна машина под длинные стороны, другая - под короткие. Плитка заходила в машину, выставлялась ровно, захватывалась сверху и снизу прижимными движущимися лентами и подавалась на калибраторы - алмазные диски, вращающиеся с большой скоростью. Шум там был!!!! Самое шумное место на предприятии. Без наушников долго не простоять.
Цель калибровки - задать плитке точный размер и точный угол.
На одной из линий стояла специальная машина по полировке плитки. Полированная плитка - это одна из разновидностей плиток со своими свойствами и особенностями. К тому же весьма проблемная в производстве.
Машина начинала с того, что…. обгрызала с плитки верхний слой. Буквально. Занимался этим специальный валик с алмазными зубьями, оставлявший на поверхности плитки борозды. За тем две шлифовальные головы убирали эти борозды. А затем начинался процесс тонкой шлифовки и окончательной полировки.
Если удавалось получить хоть какое-то количество готовой плитки, то она следовала на упаковку.
Паковал плитку робот. Но здесь были постоянные проблемы. За машиной надо было постоянно следить и подстраивать. Но это что касалось мелкой плитки. 120/60 или меньше. А вот крупную приходилось упаковывать вручную. Специальным краном с рамой и вакуумными присосками плитка снималась со стола и устанавливалась на специальные козлы.
Ну вот… Плитка произведена и упакована. Теперь бы её как-нибудь продать. А вот с этим начинались реальные проблемы…
В инфракрасной печи...
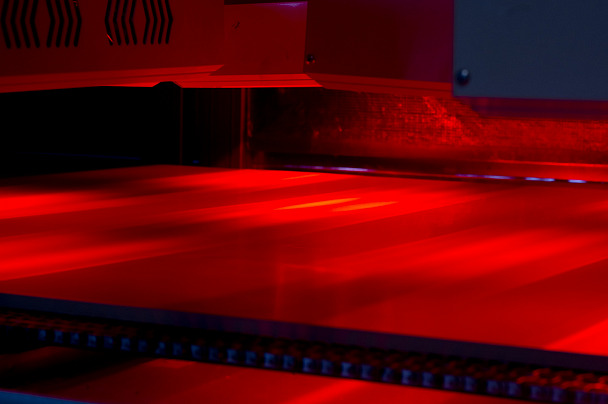
оформляем выставочный зал.
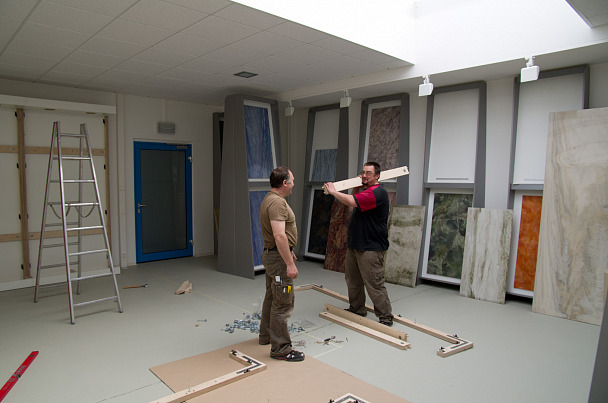
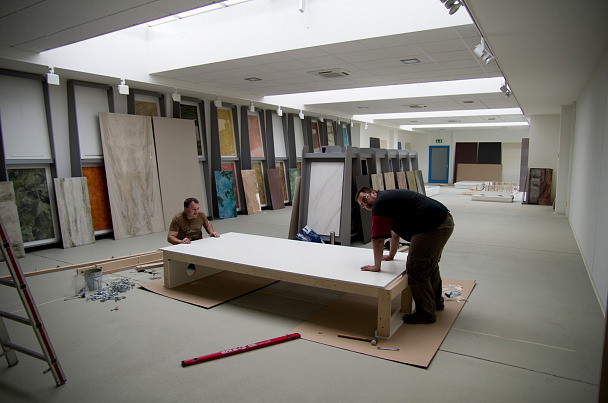